How to quickly check internal corrosion in your network
- Guillaume Labrouze
- Aug 25, 2022
- 3 min read
Updated: Sep 16, 2022

Internal #corrosion in piping and pipeline networks is a complex phenomenon that will not give any alert before a leak occurs. The complexity of internal corrosion management lies in the evolution of the fluid's composition. In an oil field for example, the production fluid which was anhydrous at the beginning can content more than 50% of water 10 years later. Sometimes, a water breakthrough in the formation can change the fluid composition in a just a couple of days.
If corrosion #risk is not carefully considered, the production team may not review the chemical treatments (corrosion inhibitors), and corresponding monitoring systems are not in place. Because this topic is usually not seen as a priority, the corrosion mechanisms start damaging the pipes.
A simple solution - Total iron content measurement
Internal corrosion management is a complex discipline because the mechanisms are various (galvanic corrosion, CO2, H2S, O2, bacteria) and the accurate monitoring tools are complex to install (coupons, probes) if not part of the original installation design.
However, there is a practical way to quickly assess the corrosion rate in a line: the measurement of total iron content. This practical approach may not be 100% accurate, but its implementation is easy, not expensive and does not require specific skills (of course, proper safety procedures and training are mandatory to collect the fluid samples).
Measurement of total iron content shows the presence of iron in the water part of the fluid. This iron may be the result of corrosion. We shall keep in mind that iron naturally comes from the formation. That is why it is highly recommended to get samples at the inlet and at outlet of a pipeline (or a process) to measure the increase of iron concentration. An increase of iron content means a corrosion process is ongoing.
A well-known product is the CHEMets kit K-6010 that allows operators to measure the total iron content in the production water. Using a simple color scale, it is easy to determine a concentration up to 10ppm.
There are two common mistakes:
Some operators consider that a single measurement at the end of a pipeline is enough. This is a nonsense as the objective is to measure the iron that “appeared” between the inlet and the outlet of a pipeline or a process unit.
Some other operators do measure the difference between the inlet and outlet and consider a threshold value between good and bad corrosion activities. This is a big mistake: the total iron content shall be linked to the water content flowrate.
A simple (and simplified) exercise
Which pipeline has the highest corrosion rate?
Remark: pipelines A and B have the same length and internal diameter.
Pipeline A:
- Total Iron Inlet: 0 ppm
- Total iron outlet: 10 ppm
- Water content: 20%
- Flow rate: 1,000 bfpd (159 m3/day)
Pipeline B:
- Total Iron Inlet: 2 ppm
- Total iron outlet: 4 ppm
- Water content: 50%
- Flow rate: 10,000 bfpd (1,590 m3/day)
Solution:
Pipeline A: (10-0) mg/L *159,000 L/day * 0.2 = 318,000 mg/day = 0.318 kg/day
Pipeline B: (4-2) mg/L*1,590,000 L/day * 0.5 = 1,590,000 mg/day = 1.590 kg/day
Pipeline B is losing 1.59 kg of iron per day (vs 0.32 kg per day for pipeline A).
Way forward
Once the corrosion activity has been assessed with total iron content method, it is time to implement deeper investigation methods and monitoring strategies. This is where #integrity specialist companies like #Sanorah provide a clear added value. For each pipeline or installation, there is a cost-optimal monitoring solution which provides the proper piece of information about the corrosion activity and how to mitigate it.
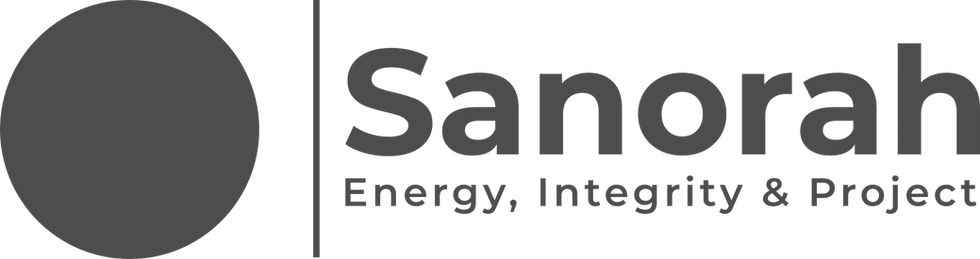
Comments